![]() |
TIAGo Safety and regulatory reference#
Safety is important when working with TIAGo. This chapter provides an overview of safety issues, general usage guidelines to maintain safety, and some safety-related design features. Before operating the robot, all users must read and understand this page!
Intended applications#
It is important to clarify the intended usage of the robot prior to any kind of operation.
TIAGo is a robotics research and development platform designed to be operated in a controlled environment, under supervision by trained staff at all times
The hardware and software of TIAGo enables research and development of activities in the following areas:
Navigation and SLAM
Manipulation
Perception
Speech recognition
Human-robot interaction
Working environment and usage guidelines#
The working temperatures are:
Robot: +10ºC ~ +35ºC
The space where TIAGo operates should have a flat floor and be free of hazards. Specifically, stair-ways and other drop offs can pose an extreme danger. Avoid sharp objects (such as knives), sources of fire, hazardous chemicals, or furniture that could be knocked over.
Maintain a safe environment:
The terrain for TIAGo usage must be capable of supporting the weight of the robot (see Specifications section). It must be horizontal and flat. Do not use any carpet, to avoid tripping over.
Make sure the robot has adequate space for any expected or unexpected operation.
Make sure the environment is free of objects that could pose a risk if knocked, hit, or otherwise affected by TIAGo.
Make sure there are no cables or ropes that could be caught in the covers or wheels; these could pull other objects over.
Make sure no animals are near the robot.
Be aware of the location of emergency exits and make sure the robot cannot block them.
Do not operate the robot outdoors.
Keep TIAGo away from flames and other heat sources.
Do not allow the robot to come in contact with liquids.
Avoid dust in the room.
Avoid the use or presence of magnetic devices near the robot.
Apply extreme caution with children.
Battery manipulation#
The following guidelines must be respected when handling the robot in order to prevent damage to the robot’s internal batteries.
Do not expose to fire.
Do not expose the battery to water or salt water, or allow the battery to get wet.
Do not open or modify the battery case.
Do not expose to ambient temperatures above 49ºC for over 24 hours.
Do not store in temperatures below -5ºC over seven days.
For long term storage (more than 1 month) charge the battery to 50%.
Do not use the TIAGo’s batteries for other purposes.
Do not use other devices but the supplied charger to recharge the battery.
Do not drop the batteries.
If any damage or leakage is observed, stop using the battery.
Leakage#
The battery is the only component of the robot that could potentially leak. To avoid leakage of any substance from the battery, follow the instructions of Robot storage recommandations, to ensure the battery is manipulated and used correctly.
Firefighting equipment#
For correct use of TIAGo in a laboratory or location with safety conditions, it is recommended to have in place a C Class or ABC Class fire extinguisher (based on halogenated products), as these extinguishers are suitable for stifling an electrical fire.
If a fire occurs, please follow these instructions:
Call the firefighters.
Push the emergency stop button, as long as you can do so without any risk.
Only tackle a fire in its very early stages.
Always put your own and others’ safety first.
Upon discovering the fire, immediately raise an alarm.
Make sure the exit remains clear.
Fire extinguishers are only suitable for fighting a fire in its very early stages. Never tackle a fire if it is starting to spread or has spread to other items in the room, or if the room is filling with smoke.
If you cannot stop the fire or if the extinguisher runs out, get yourself and everyone else out of the building immediately, closing all doors behind you as you go. Then ensure the fire brigade are on their way.
Turning on/Shutting down the robot#
FOllow the process described in TIAGo power management and docking.
Preventing falls#
TIAGo has been designed to be statically stable, even when the arms are holding their maximum payload in their most extreme kinematic configuration. Nevertheless, some measures need to be respected in order to avoid the robot from tipping over.
Measure 1#
Do not apply external downward forces to the arms when they are extended in the direction shown in figure below:
Measure 2#
Do not navigate when the arms are extended, especially when the torso is also extended, see figure below:
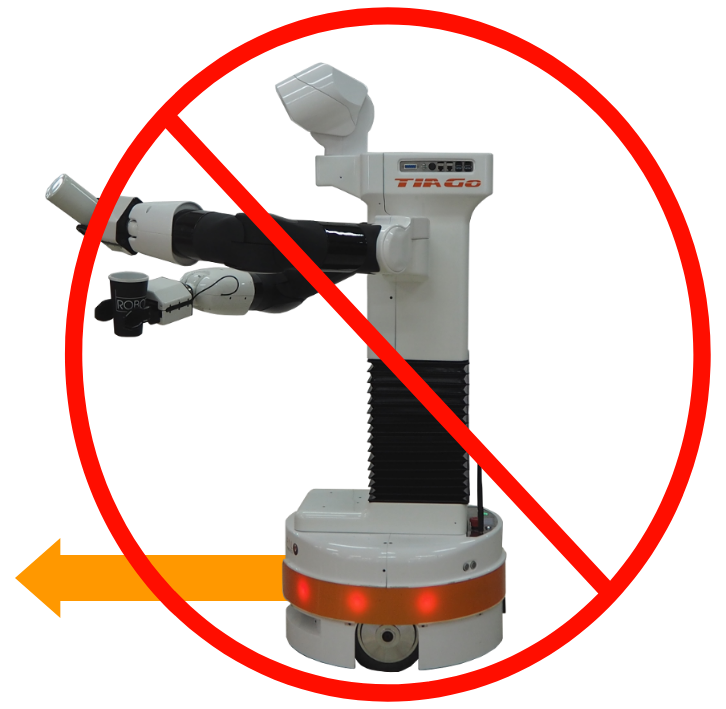
Figure: Avoid navigation with arms and torso extended#
Measure 3#
TIAGo has been designed to navigate in flat floor conditions. Do not navigate on floors with unevenness higher than 5%, see figure below:
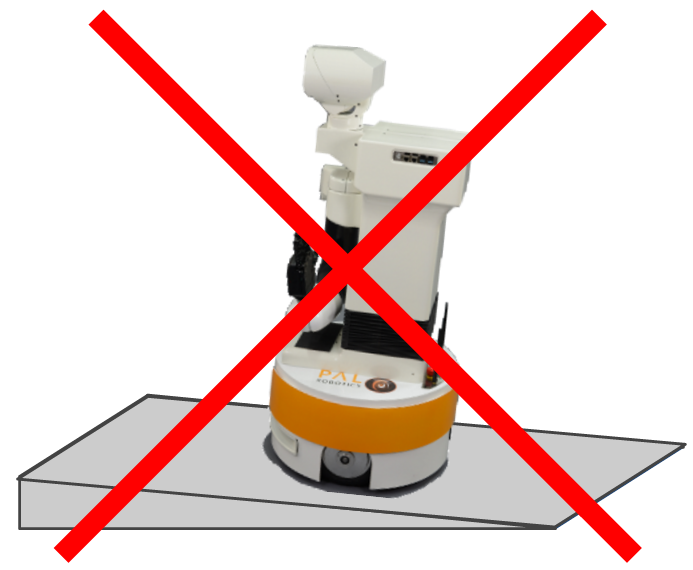
Figure: Navigation on ramps is not recommended#
Measure 4#
Avoid navigating close to downward stairs, as TIAGo’s laser range-finder will not detect this situation and the robot may fall down the stairs.
Measure 5#
In order to maintain safety, it is highly recommended to navigate with the arms folded and the torso at a low extension, like in the predefined Home configuration, see figure below. This pose provides the following advantages:
Reduces the robot’s footprint, lowering the probability that the arms collide with the environment
Ensures the robot’s stability as the center of mass is close to the center of the robot and it is kept low
Preventing collisions#
Most collisions occur when moving TIAGo’s arms. It is important to take the following measures into account in order to minimize the risk of collisions.
Measure 1#
Make sure that there are no obstacles in the robot’s surroundings when playing back a predefined motion or moving the joints of the arms. Provided that the maximum reach of the arm is 86 cm without the end-effector, a safe way to move the arms is to have a clearance around the robot of about 1.5 m.
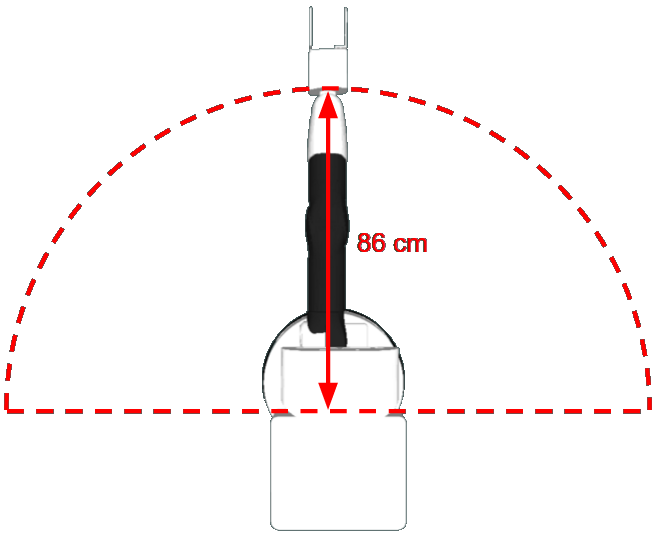
Figure: TIAGo arm reach#
Measure 2#
Another active measure that could mitigate damage due to collisions is the
collision detector
node. This is found in the startup extras tab of the Web
Commander. This is, in fact, an example of how to implement safety using
feedforward current control. When enabled, this node monitors the current
consumption of the seven joints of the arms. If a joint is consuming more than a
given threshold, it stops the motion. Note that when this node is running,
the arms will not be able to handle some heavy objects as the extra payload
could cause extra current consumption in some joints. This would abort the
specific motion. It is also worth noting that the gravity compensation mode
generates some noise in the current when changing from current to position
control. In such a case, if the collision detector
is activated, this can
trigger the abortion of the motion. This safety measure is not available when
the Whole Body Control is running. It is important to remark that this node
should not be used as a final safety measure. This is just an example and is
not fully tested as such.
How to proceed when an arm collision occurs#
Warning
As prevention measure, when doing movements with TIAGo’s arms it is strongly recommended that there are two people overseeing the robot and ready to react in case of need of an emergency stop.
When any of the arms collide with the environment, see Figure: Example of arm collision onto a table, the motors of the arm will continue exerting force, which may cause potential damage to the environment or the arm covers. Serious damage to the motors will not occur, as they have integrated self-protection mechanisms to detect over-heating and overcurrent which switches them off automatically if necessary. Nevertheless, in order to minimize potential harm to the environment and to the robot, the following procedure should be undertaken, as depicted in Figure: How to proceed when a collision occurs:
Press the emergency button to power off the robot’s motors. The arms will fall down, so be ready to hold the wrists while the emergency button remains activated
Move the robot out of the collision by pushing the mobile base and pulling the arm to a safe place
Release the emergency button by rotating it clockwise according to the indications on the button until it pops out. When the On/Off button flashes, press it for 1 second
The power and control mode of the motors are restored and the robot is safe and operational
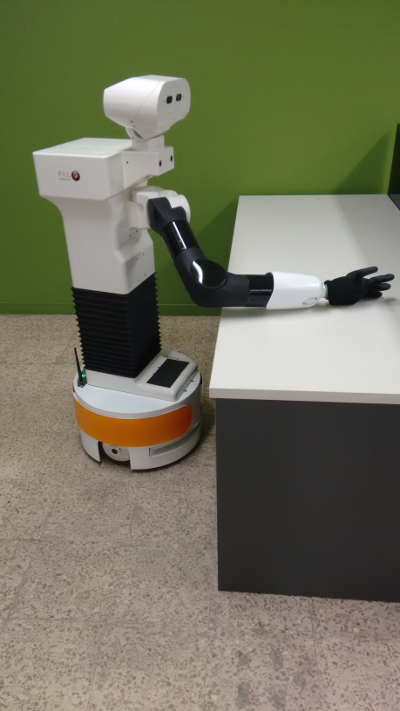
Figure: Example of arm collision onto a table#
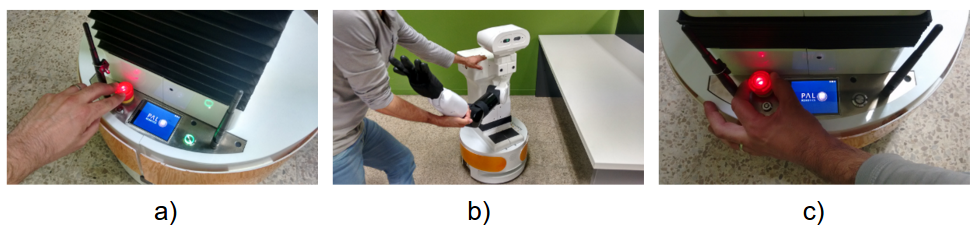
Figure: How to proceed when a collision occurs#
Omindirection wheels#
Note
This section is only relevant to the robots equipped with the omnidirectional mobile base.
In order to guarantee and preserve the proper operation of the mecanum wheels of the robot, check periodically that all the screws of the small rollers of the wheels are tight and clean at the point they can rotate freely. In case a screw looks loose, before operating again the robot, tighten the screw and make sure that the roller is able to freely rotate on its axis.
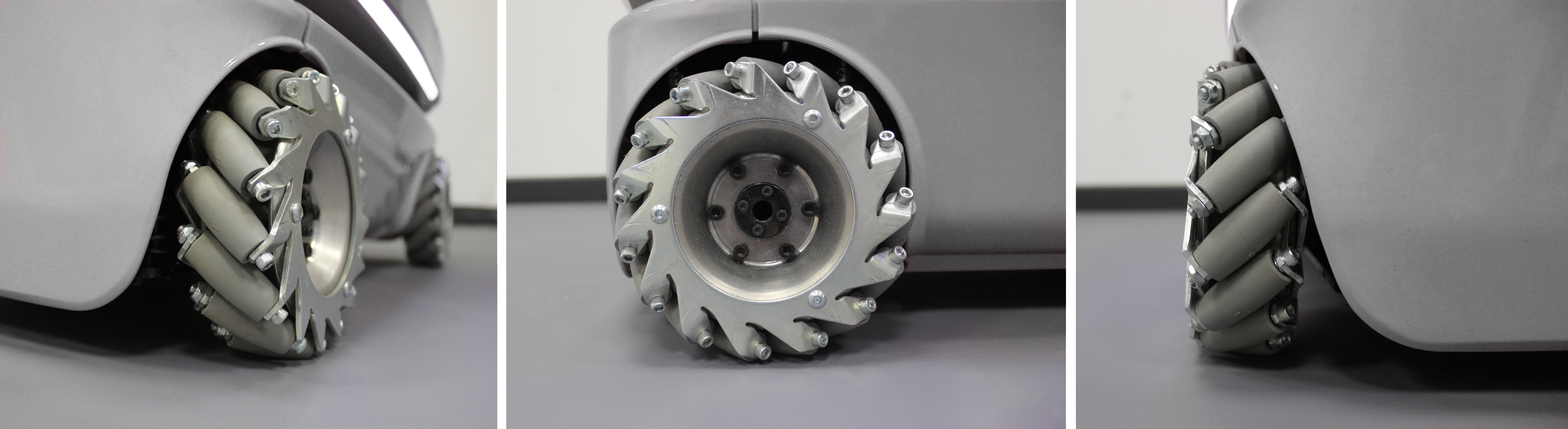
Figure: Detailed view of the mecanum wheels and their rollers#