Omnidirectional mobile base#
TIAGo’s mobile base is provided with a omnidirectional drive mechanism and contains an onboard computer, batteries, power connector, two laser range-finders, a user panel, a service panel and wireless connectivity. Furthermore, the version of TIAGo with a docking station has a charging plate on the front.
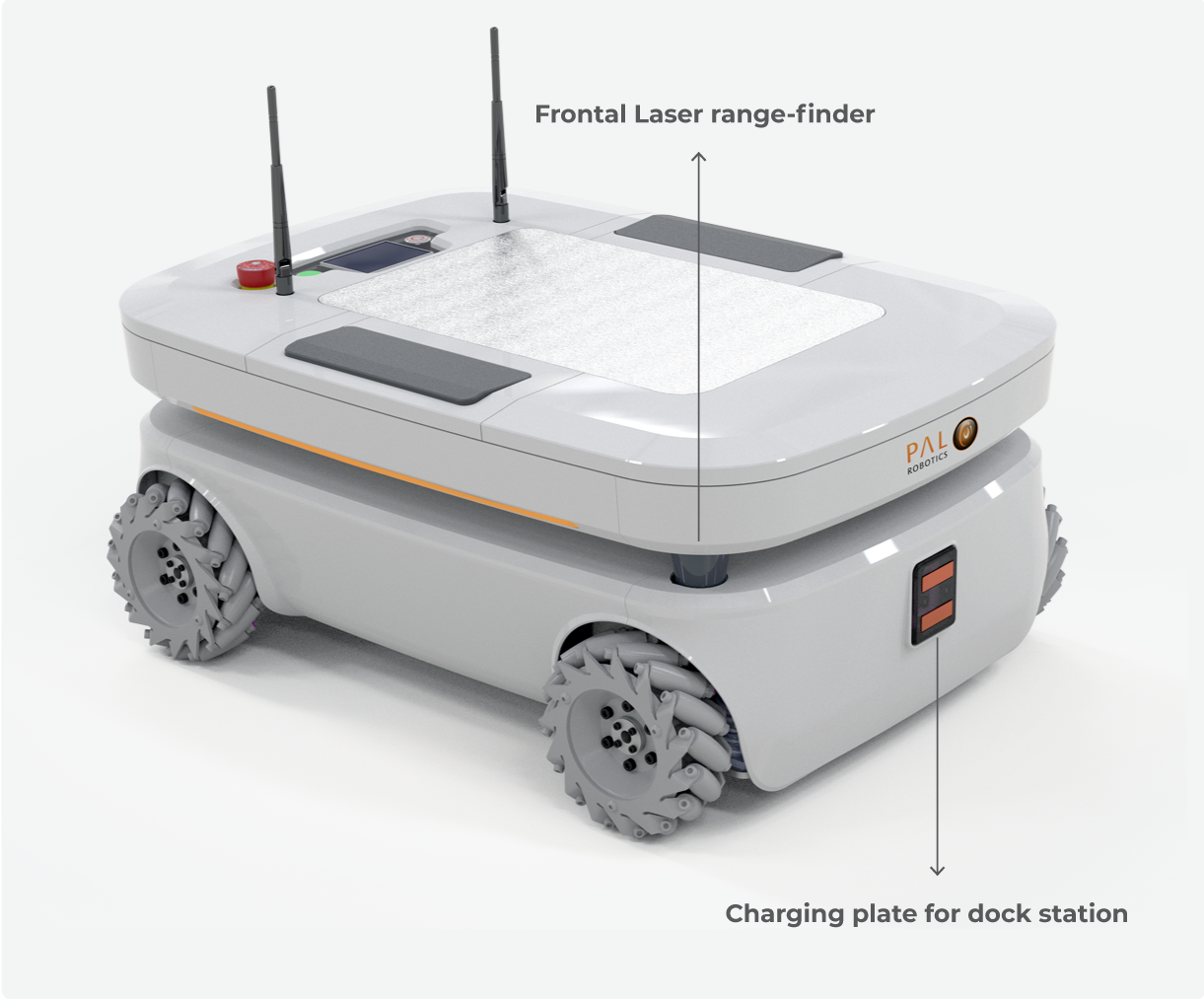
Figure: Mobile base front view#
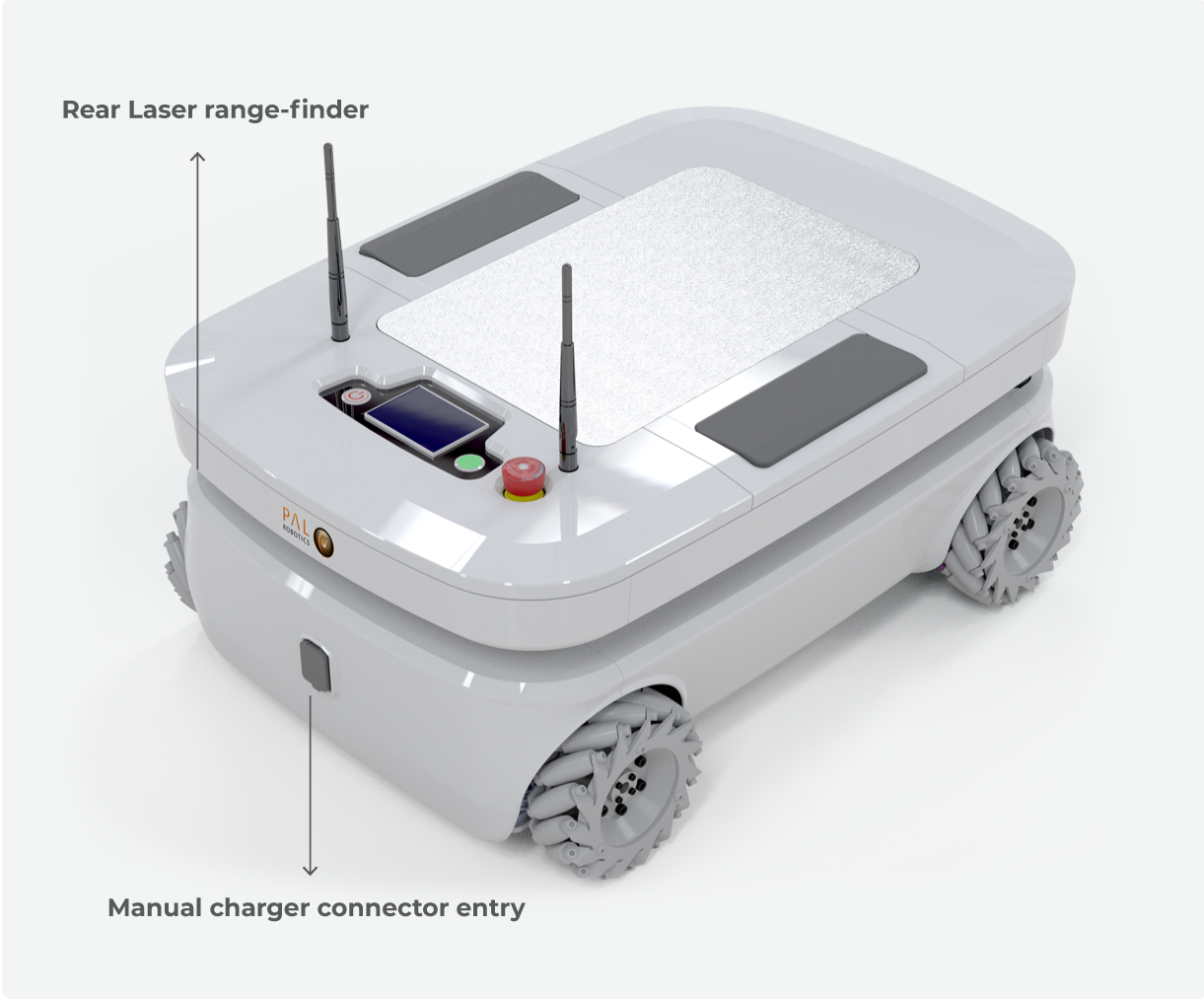
Figure: Mobile base rear view#
Robot’s main specifications#
The robot features an omnidirectional drive system. It is powered by two batteries, ensuring robust performance for various tasks.
Height |
31 cm |
Weight |
48 Kg |
Base footprint |
72 * 50 cm |
Drive system |
Omnidirectional |
Max speed |
1 m/s |
Payload |
150 Kg |
Battery |
2 x 36 V, 20 Ah |
Features of the omnidirectional mobile base#
Onboard computer#
The specifications of TIAGo ‘s onboard computer depends on the configuration options you have ordered. The different possibilities are shown in table below:
Component |
Description |
---|---|
CPU |
Intel i5 / i7 |
RAM |
8 / 16 GB |
Hard disk |
250 / 500 GB SSD |
Wi-Fi |
802.11 a/b/g/n/ac |
Bluetooth |
Smart 4.0 Smart Ready |
Battery#
The specifications of the battery supplied with TIAGo are shown in table below:
Type |
Li-Ion |
---|---|
V_nominal |
36.0 V |
V_max |
42.0 V |
V_cutoff |
30.0 V |
Nominal capacity |
20 Ah |
Nominal energy |
720 Wh |
Max. continuous discharge current |
20 A |
Pulse discharge current |
60 A |
Max. charging current |
15 A |
Charging method |
CC/CV |
Weight |
7.5 kg |
TIAGo’s base can be equipped with two batteries. In this case, the total Nominal capacity is 1440 Wh.
Power connector#
TIAGo must only be charged only with the supplied charger. To insert the charger connector, open the lid located on the rear part of the robot, as shown in Figure: Connector entry.
Connection Insert charging connector with metal lock facing up and push it, as shown in Figure: Connector entry b , until you hear a ‘click’.
Disconnection Once charge is completed, connector can be removed. In order to o remove it, press metal lock and pull the connector firmly, see Figure: Connector entry.
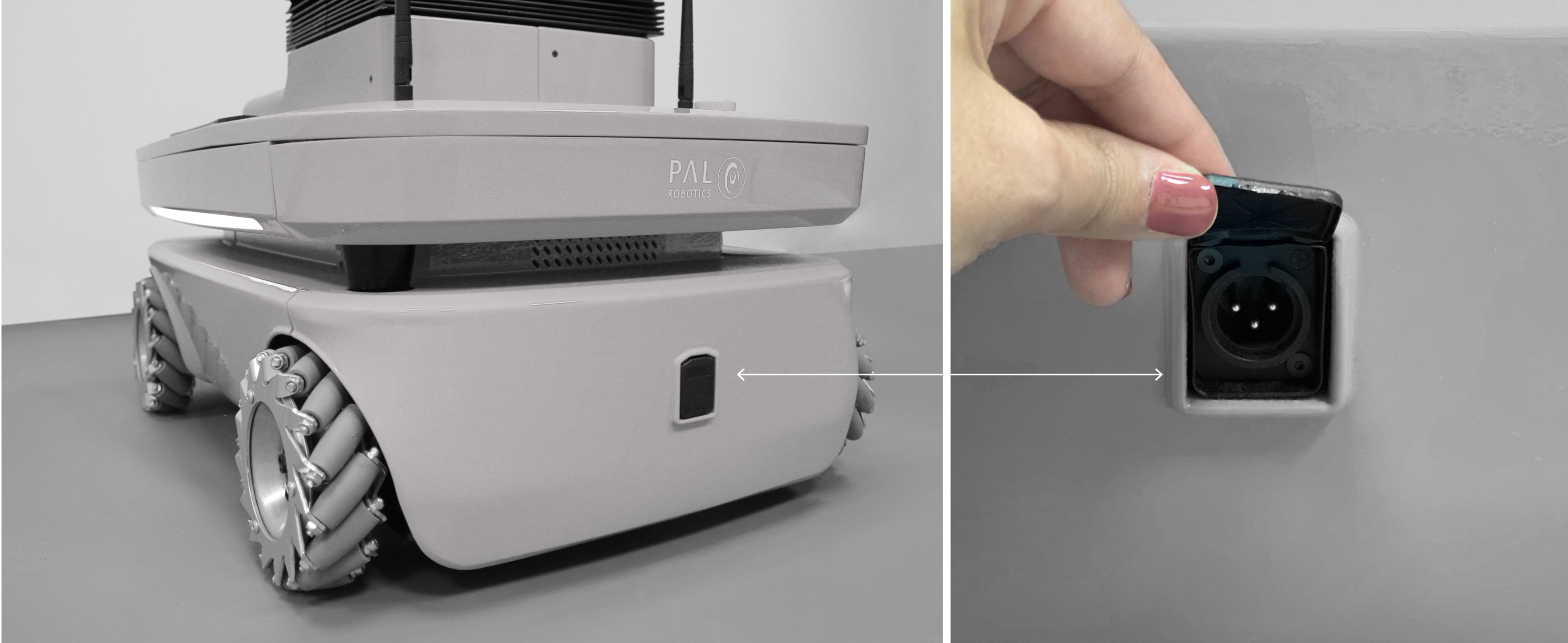
Figure: Connector entry#
Laser range-finder#
The specifications of the laser on the front part of the mobile base depend on the configuration options you have ordered. The lasers supported are shown in table:
Manufacturer |
Hokuyo |
---|---|
Model |
URG-04LX-UG01 |
Range |
0.02 - 5.6 m |
Frequency |
10 Hz |
Field of view |
180 degrees |
Step angle: |
0.36 degrees |
Manufacturer |
SICK |
---|---|
Model |
TIM561-2050101 |
Range |
0.05 - 10 m |
Frequency |
15 Hz |
Field of view |
180 degrees |
Step angle: |
0.33 degrees |
Manufacturer |
SICK |
---|---|
Model |
TIM571-2050101 |
Range |
0.05 - 25 m |
Frequency |
15 Hz |
Field of view |
180 degrees |
Step angle: |
0.33 degrees |
IMU#
The Inertial Measurement Unit is mounted at the center of the mobile base and may be used to monitor inertial forces and attitude. The specifications are presented in the table:
Manufacturer |
InvenSense |
---|---|
Model |
MPU-6050 |
Gyroscope |
3-axis |
Accelerometer |
3-axis |
User panel#
The user panel is on the top, rear part of TIAGo mobile base. It provides the buttons to power up and shutdown the robot, and a screen to give visual feedback on the robot’s status. All the specific elements of the user panel are shown in the figure below and the description of each element is presented in the table below:
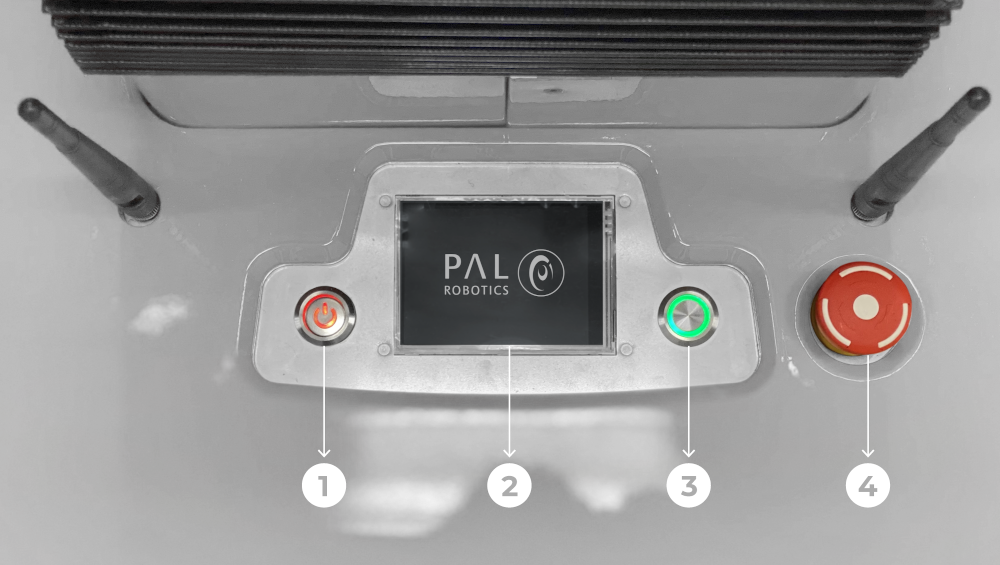
Figure: User panel#
Number |
Name / Short description |
---|---|
1 |
Electric switch |
2 |
Information display (optional) |
3 |
On / Off button |
4 |
Emergency stop |
Electric switch The electric switch is the main power control switch. Before turning TIAGo ON make sure first that this switch is ON, i.e. its red light indicator is ON. On the other hand, when TIAGo is not going to be used for a long period, please press the switch so that its red light indicator turns OFF. Note that this switch should not be turned OFF before using the On/Off button to turn OFF the onboard computer of the robot. Turning OFF this switch will cut instantaneously the power supply to all the robot components, including the onboard computer. Do not use this switch as emergency stop. For the emergency stop please refer to the next section.
Emergency stop When pushed, motors are stopped and disconnected. The green indicator of the On/Off button will blink fast in order to notify the user of the emergency state.
To start normal behaviour again, a two step validation process must be executed: the emergency button must be released by rotating clockwise, and then the On/Off button must be pressed for one second. The green light indicator of the On/Off button will change to a fixed state.
Information display 320x240 Color TFT display shows the battery level on the top right corner.
On / Off button he standby control button is a pushbutton with a green light that indicates the system’s current status.
Light |
State |
Name / Short description |
---|---|---|
Off |
Fixed |
Standby |
On |
Fixed |
Running |
On |
Slow-Blink |
System in process of shutdown |
On |
Fast-Blink |
Emergency state |
After main power is connected, i.e. electric switch is ON (Figure: User panel), user must press this button during 1 second in order to start the TIAGo.
To re-set the system in standby mode when the robot is running, press the button again. The green light will blink slowly during shutdown procedure and light-off when standby mode reached.
Service panel#
It is possible to access the service panel by removing the cover behind the laser (see figure Figure: Service panel).
This service panel gives access to video, usb and On/Off button of the robot’s computer. It can be used for reinstallation or debug purposes.
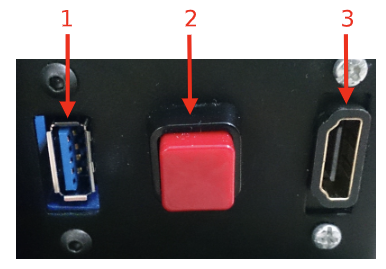
Figure: Service panel#
Number |
Name / Short description |
---|---|
1 |
USB 3.0 |
2 |
On/Off button computer |
3 |
HDMI |
Expansion panel#
In order to access this panel the top plate of the robot must be removed.
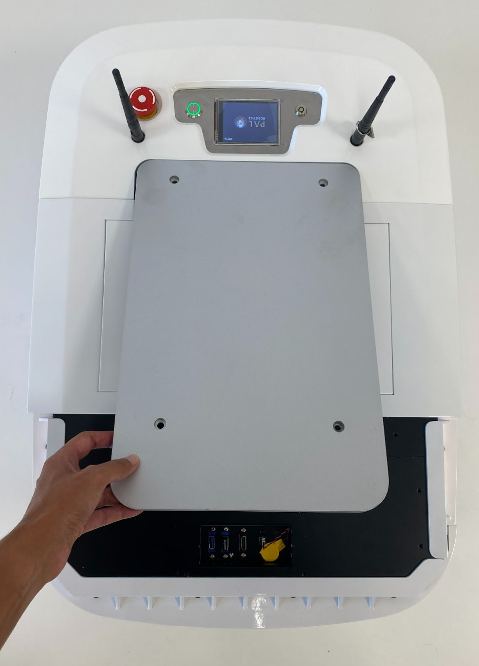
Figure: Expansion panel omni base access#
Mounting plate must be removed in order to get access to this panel.
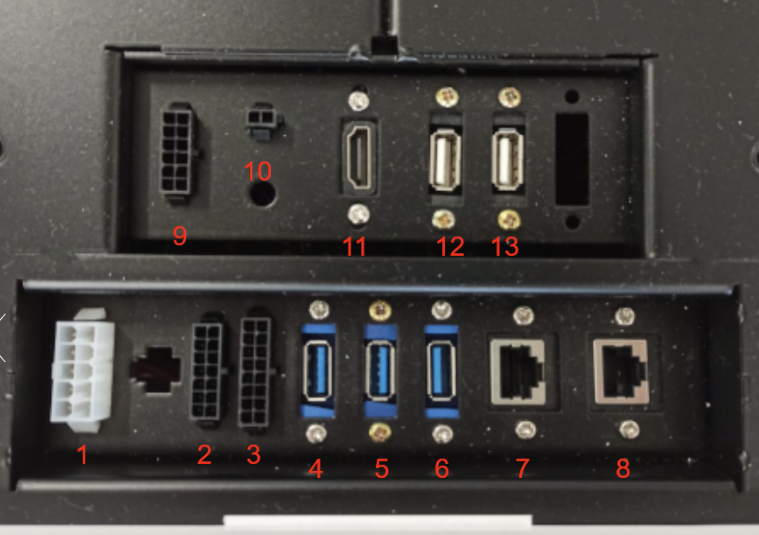
Figure: Expansion panel omni base detail#
Number |
Name / Short description |
---|---|
1 |
Power connector |
2 |
Communications Expansion, i.e. CAN (if ordered) |
3 |
GPIOs |
4 |
USB 3.0 |
5 |
USB 3.0 |
6 |
USB 3.0 |
7 |
Ethernet |
8 |
Ethernet |
9 |
Reserved |
10 |
Speaker |
11 |
HDMI |
12 |
USB 2.0 |
13 |
USB 2.0 |
Power connector
This expansion connector provides access to the battery and provide up to 360 W. Battery voltage can vary depending on actual State Of Charge in the range of 30V to 42V.
It is recommended to use the all 3 battery output pins in parallel to divide current between them. The maximum current that can be provided through these battery pins is 10 A in total, approximately.
Connector type Molex 39012101, mating part is Molex 39012100.
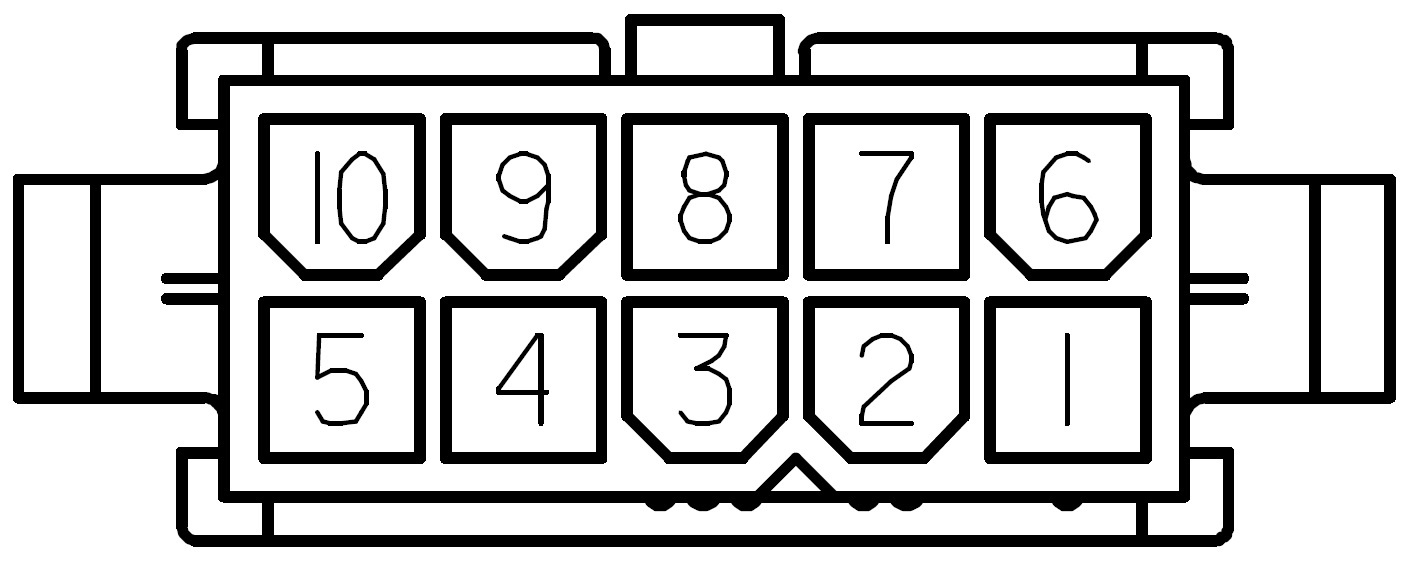
Figure: Power Expansion Connector Pinnout#
Pin |
Name / Short description |
---|---|
1 |
|
2 |
+12V output (max 4.5A shared with SICK Laser if present) |
3 |
Battery output (max 9A/pin) |
4 |
Battery output (max 9A/pin) |
5 |
Battery output (max 9A/pin) |
6 |
|
7 |
GND of 12V output |
8 |
Battery GND |
9 |
Battery GND |
10 |
Battery GND |
Comunication expansion
This expansion connector provides access to internal communication buses of the robot. There are 2 CAN buses for motors and actuators and a propietary bus for sensors. Only the CAN buses are available to the user. CAN bus speed is 1Mbit/s. Connector type Molex 43020-1400, mating part is Molex 43025-1400.
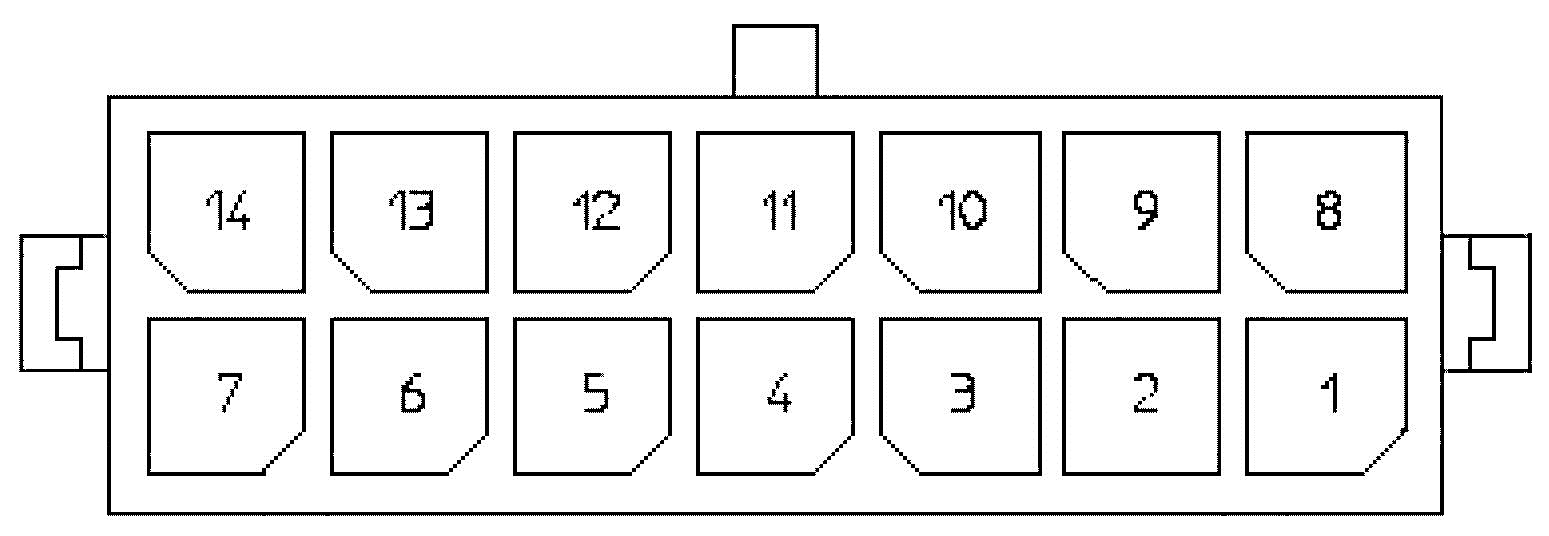
Figure: Communication expansion connector pinout#
Pin |
Name / Short description |
---|---|
1 |
CANL of LEFT bus |
2 |
Shield of LEFT bus |
3 |
CANH of LEFT bus |
4 |
reserved |
5 |
reserved |
6 |
reserved |
7 |
n.c. |
8 |
CANL of RIGHT bus |
9 |
Shield of RIGHT bus |
10 |
CANH of RIGHT bus |
11 |
reserved |
12 |
reserved |
13 |
reserved |
14 |
reserved |
GPIOS
This expansion connector provides access to General Purpose Input (GPI) and Output (GPO) pins.
Connector type Molex 43020-1600, mating part is Molex 43025-1600.
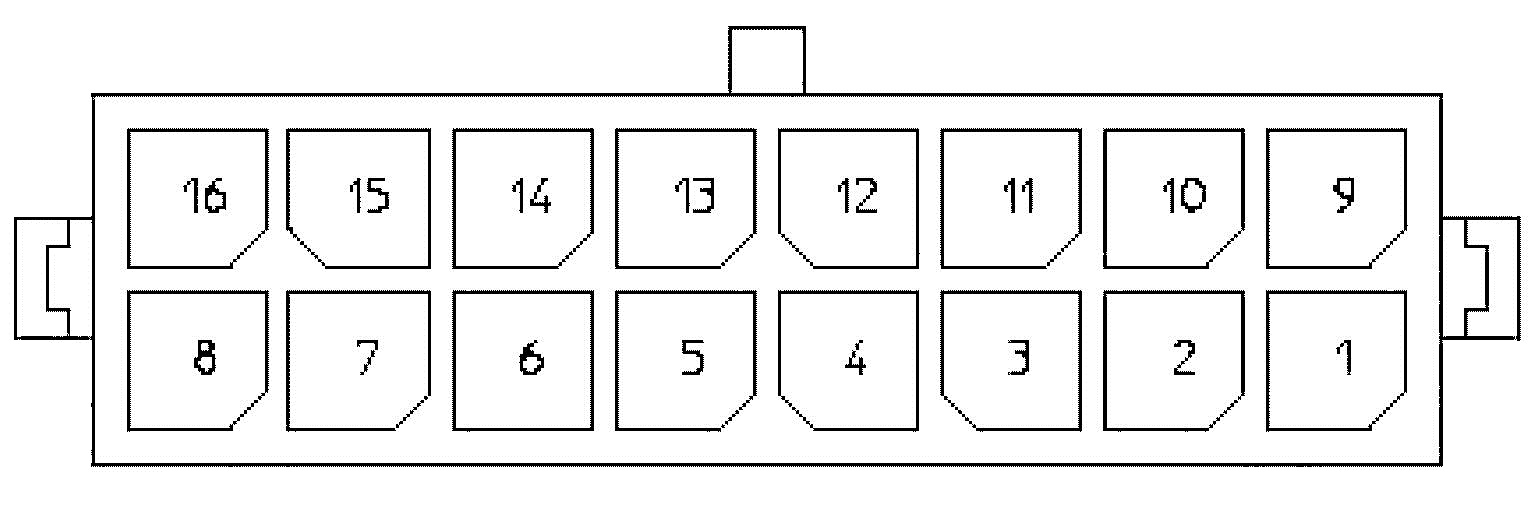
Figure: GPIOs connector pin description#
Pin |
Name / Short description |
---|---|
1 |
|
2 |
|
3 |
|
4 |
5V |
5 |
GPO 0 (5V TTL level) |
6 |
GPO 1 (5V TTL level) |
7 |
GPO 2 (5V TTL level) |
8 |
GPO 3 (5V TTL level) |
9 |
|
10 |
|
11 |
|
12 |
GND |
13 |
GPO 0 (5V TTL level) |
14 |
GPO 1 (5V TTL level) |
15 |
GPO 2 (5V TTL level) |
16 |
GPO 3 (5V TTL level) |
General purpose outputs are referenced to pin 12 GND and by default are set to low level. On the other hand, general purpose inputs must be set using pin 4 +5V for high level and pin 12 GND for low level, and have an internal default pull-up.
Connectivity#
TIAGo is equipped with a dual band Wireless 802.11b/g/n/ac interface, plus bluetooth 4.0 and a WiFi antenna. When the WiFi interface is configured as access point, it has a 802.11g interface.
There are two Gigabit Ethernet ports, ports 2 and 3 in the expansion panel figure, that can be used to connect to the robot’s internal network. For this network, the IP address range 10.68.0.0/24 has been reserved.
Caution
The IP addresses used in the building network MUST not use this range because it can interfere with the robot’s services.
Electrical parts and components#
Neither TIAGo OMNI Base nor any of its electrical components or mechanical parts are connected to external ground. The chassis and all electromechanical components are physically isolated from the ground by the isolation rubber under its feet. Avoid touching any metal parts directly to prevent discharges and damage to TIAGo OMNI Base’s electromechanical parts.
Electrical power supply and connectors
The power source supplied with TIAGo OMNI Base is compliant with the Directive on the restriction of the use of certain hazardous substances in electrical and electronic equipment 2002/95/EC (RoHS) and with the requirements of the applicable EC directives, according to the manufacturer. The power source is connected to the environment ground, whenever the supplied wire is used (Phase-Neutral-Earth).